Porosity in Welding: Identifying Common Issues and Implementing Best Practices for Avoidance
Porosity in welding is a prevalent problem that commonly goes undetected till it creates substantial troubles with the stability of welds. In this discussion, we will certainly check out the essential factors adding to porosity formation, analyze its harmful effects on weld performance, and discuss the best practices that can be taken on to decrease porosity event in welding procedures.
Typical Reasons For Porosity
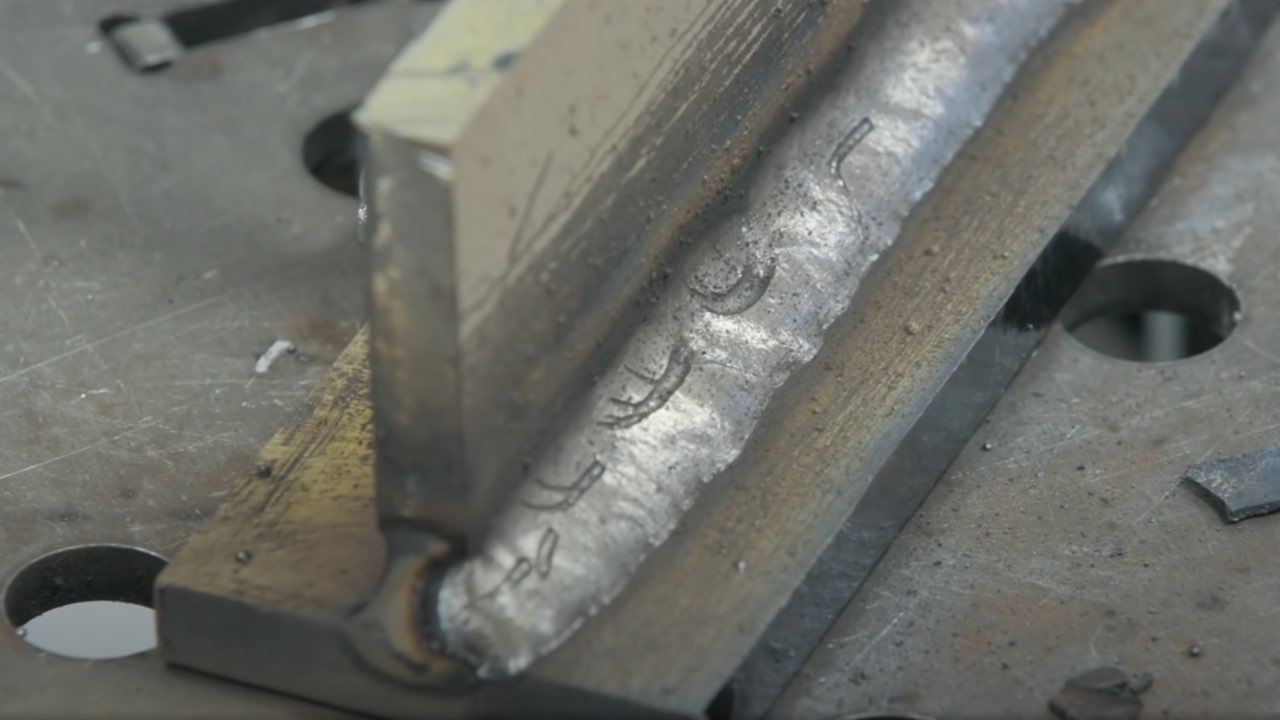
Another constant perpetrator behind porosity is the presence of impurities externally of the base metal, such as oil, oil, or rust. When these impurities are not successfully removed prior to welding, they can vaporize and become caught in the weld, causing issues. Utilizing unclean or damp filler products can introduce impurities into the weld, adding to porosity problems. To minimize these common root causes of porosity, extensive cleansing of base steels, correct securing gas option, and adherence to optimum welding parameters are important practices in accomplishing high-grade, porosity-free welds.
Influence of Porosity on Weld Top Quality

The visibility of porosity in welding can dramatically endanger the structural integrity and mechanical residential or commercial properties of welded joints. Porosity develops gaps within the weld steel, compromising its total strength and load-bearing capability. These spaces act as stress and anxiety focus points, making the weld more susceptible to fracturing and failure under applied lots. Furthermore, porosity can minimize the weld's resistance to rust and various other ecological aspects, better lessening its long life and efficiency.
Among the key effects of porosity is a decrease in the weld's ductility and strength. Welds with high porosity degrees have a tendency to exhibit reduced effect stamina and decreased ability to flaw plastically prior to fracturing. This can be especially concerning in applications where the welded parts undergo dynamic or cyclic loading conditions. Furthermore, porosity can restrain the weld's anchor capability to efficiently transmit pressures, causing premature weld failure and possible security hazards in vital structures.
Best Practices for Porosity Prevention
To improve the structural stability and quality of welded joints, what specific actions can be executed to lessen the event of porosity during the welding procedure? Porosity prevention in welding is vital to ensure the stability and toughness of the final weld. One efficient technique appertains cleansing of the base steel, eliminating any kind of contaminants such as rust, oil, paint, or wetness that can result in gas entrapment. Making sure that the welding equipment is in great problem, with tidy consumables and suitable gas flow prices, can additionally considerably minimize porosity. In addition, maintaining a stable arc and managing the welding criteria, such as voltage, existing, and travel speed, assists produce a regular weld swimming pool that minimizes the risk of gas entrapment. Utilizing the right welding strategy for the details material being welded, such as adjusting the welding angle and gun setting, can additionally protect against porosity. Normal inspection of welds and immediate removal of any type of problems identified throughout the welding process are crucial methods to stop porosity and produce top notch welds.
Significance of Correct Welding Techniques
Carrying out correct welding techniques is vital in ensuring the structural stability and top quality of welded joints, developing upon the structure of reliable porosity prevention procedures. Welding strategies straight impact the general toughness and toughness of the bonded structure. One essential element of proper welding strategies is preserving the correct warm input. Excessive warmth can result in increased porosity because of the entrapment of gases in the weld pool. Alternatively, insufficient warmth may cause incomplete blend, creating possible weak points in the joint. In addition, using the ideal welding parameters, such as voltage, existing, and travel speed, is crucial for accomplishing audio welds with very little porosity.
Additionally, the option of welding procedure, whether it be MIG, TIG, or stick welding, need to align with the particular demands of the task to ensure optimal results. Appropriate cleansing and prep work of the base metal, along with selecting the best filler product, are additionally necessary parts of proficient welding techniques. By adhering to these finest methods, welders can lessen the danger of porosity development and generate high-grade, structurally audio welds.
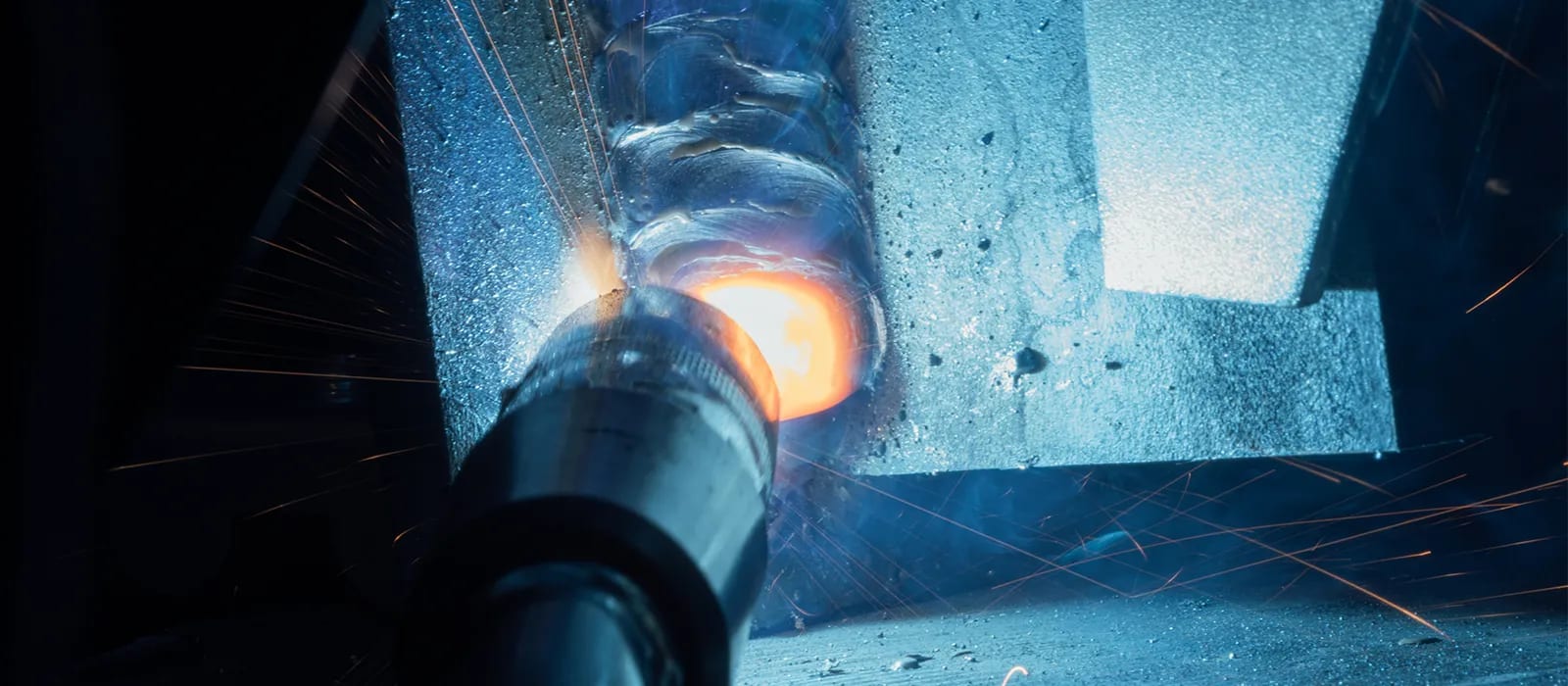
Testing and Quality Control Steps
Checking procedures are vital to discover and avoid porosity in welding, ensuring the stamina and durability of the final informative post item. Non-destructive screening methods such as ultrasonic testing, radiographic testing, and visual inspection are commonly used to recognize potential problems like porosity.
Post-weld examinations, on the various other hand, examine the final weld for any issues, consisting of porosity, and verify that it satisfies specified criteria. Carrying out a detailed quality control plan that consists of complete testing procedures and examinations is vital to minimizing porosity issues and making certain the general quality of bonded joints.
Final Thought
To conclude, porosity in welding can be an usual problem that impacts the top quality of welds. By determining the common causes of porosity and executing finest practices for avoidance, such as proper welding strategies and testing actions, welders can make sure excellent browse this site quality and trusted welds. It is necessary to prioritize prevention methods to reduce the event of porosity and preserve the honesty of welded frameworks.
Comments on “What is Porosity in Welding: Understanding Its Reasons and Enhancing Your Abilities”